|
What is Purchasing?
Definition
The nomenclature used for purchasing related activities can be quite confusing. In one environment a particular set of activities is known as "Purchasing", in another exactly the same set of activities is known as "Procurement" and in another it's known as "Category Management" or "Sourcing". So in any new environment, one of the first things to do is to understand what is meant by their particular nomenclature .
The Purchasing / Procurement / Sourcing to Payment Process (P2P)
The entire end to end process, most often referred to as Purchase to Pay (P2P) is broken down into two very different constituent parts:
- Low volume / high complexity supplier sourcing, tendering, negotiation and contracting "Source to Contract" Projects (also known as "Purchasing", "Procurement", "Sourcing" and "Category Management") to deliver substantial value improvements (most often cost savings). This part of the process is normally carried out within a dedicated team of professionals (see CIPS), where ownership for categories (sometimes also called commodities) of expenditure is allocated amongst team members.
- High volume / low complexity "Requisition to Pay" Transactions (also known as "Supply") where users throughout the business place any number of Purchase Orders (POs), once a contract has been negotiated with a supplier within the "Source to Contract" process. These activities require no professional expertise to conduct.
"Requisition to Pay" or "Supply" transactions are then further sub-divided into:
2a "Requisition to Pay" (R2P) for Indirect Purchases or General Expenses Goods/Services (i.e. those purchases common across all businesses) e.g. stationery, IT hardware & software, travel, auditors, consultancy, company cars, facilities management etc. and;
2b "Requirement to Pay" (R2P) for Direct Purchases (Raw Materials / Components / Sub-Systems / Products), those ordered by manufacturing businesses to make products.
1. Source to Contract
This part of the P2P process is more commonly referred to as Purchasing, Procurement, Sourcing, or Category Management (although historically "Procurement" was used to describe the transactional "Requisition to Pay" process). It can be performed with a strategic approach characterised by the process, known as Strategic Sourcing, Strategic Procurement, Strategic Purchasing (or Category Management) or by ommitting strategic elements of the process, the process is known as Tactical Sourcing / Procurement or Purchasing. The more rigorous Strategic process takes longer, but delivers higher value results. The strategic version of the process will typically involve segmenting suppliers using a Kraljic matrix and selectively applying appropriate approaches for each segment of the 2x2 matrix.
2a. "Requisition to Pay" (R2P) for Indirect or General Expenses Goods/Services
Increasingly referred to as the "Requisition to Pay" (R2P) process, the following steps are typical of a transactional purchasing process in an indirect or general expenses goods/services environment.
These are typically sub-divided into transactions which are authorised:
2a.1 before the order is placed; "Before the Event" or
2a.2 not authorised before the order is placed (but reviewed afterwards) "After the Event"
2a.1 Authorisation "Before the Event"
The following is an example of an ordering transaction which is authorised before the order is placed.
- A requirement for goods / services is identified by a User
- User prepares a Requisition for goods/services
- Requisition is submitted for authorisation to the Budget Holder
- If Requisition is approved, Purchase Order (PO) is issued to supplier
- Goods/Services are delivered by the Supplier
- The User confirms Receipt of Goods/Services
- Invoice is received from the Supplier
- Three way match (PO + Receipt + Invoice)
- Payment of supplier
Here's an example of a process flow chart for a "Requisition to Payment" (R2P) process for higher value transactions from the "Example Purchasing Intranet" (see Menu Links) on this website, based upon this model.
Follow this link to a "Requisition to Payment" (R2P) process flow for lower value transactions. This too is an example of an ordering transaction which is authorised by the Budget Holder "before the event" (2a1).
2a.2 Authorisation "After the Event"
For the very lowest value transactions however, a credit card process can be used; where because of the lower value and therefore lower risk nature of orders, the delay and cost of the pre-order authorisation step is avoided, and what would have been hundreds of invoices for indivudal orders are consolidated onto a single credit card statement. If any unexpected ordering behaviours are discovered by reviewing the credit card statements "after the event", ordering privileges can be withdrawn, without a substantial risk of damage to the business. BOC developed the process.
2b "Requirement to Pay" (R2P) for Direct Purchases (Raw Materials / Components / Sub-Systems / Products) for a Manufacturing Business
This is a transactional ordering process for raw materials / components / sub-systems / products in a manufacturing businesses. The main difference between it and the above transactional processes for indirect purchases, is that the "Authorisation of Requisition" step is most usually deemed to have occurred, when the Master Production Schedule (MPS) - the schedule of products to be manufactured period by period, is agreed by the Operations Director. As such, there is no need for a separate authorisation step for each raw material / component etc. needed to make the parent product, whose manufacture has been scheduled in the MPS.
Broadly speaking the process follows this approach:
- Requirement for Raw Material / Component / Sub-System / Product is generated from the MPS
- Item has/will have available inventory (Yes/No) ?
- If "No", issue Purchase Order (PO)
- Confirmation of Goods Receipt
- Receipt of Invoice
- Three way match (PO + Goods Receipt + Invoice)
- Payment
Go back to the Home Page ? Residential Care Home in Bristol
© www .interim-management-purchasing.co.uk December 2012 |
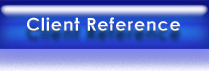
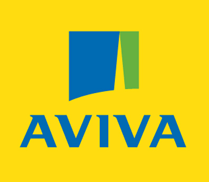
“David worked for Aviva Health UK...as Interim Head of Procurement & P2P...leading the development and implementation of procurement strategy".
David is an experienced procurement professional who has made a significant contribution to the development of procurement strategy within Aviva Health UK".
"He is intelligent and articulate and demonstrates a high level of commitment and integrity".
Full reference 
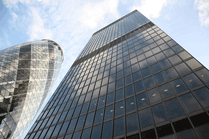
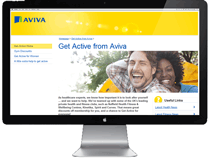
|