The BOC Procurement Card / Purchasing Card Case Study
The Introduction of a Procurement Card / Purchasing Card System For Routine Low Value Purchases
The following is a copy of the BOC case study about the development of procurement cards (or purchasing cards). It dates from the early 90s and is valuable for communicating some of the key principles. Despite the fact that we may not agree entirely with all of the nuances of this particular implementation, it remains a classic example of "thinking outside the box" when re-engineering business processes. Purchasing cards have come a long way since then; not least because of the approach to reclaiming VAT; which wasn't addressed by this project.
Contemporary Procurement Card / Purchasing Card Implementations
Follow this link for a more contemporary approach to implementing procurement cards / purchasing cards.
Introduction
The BOC Group contributes to the economies of some 60 countries. It has a global workforce of 37,000 people and achieved sales in excess of £2.8 billion in 1993.
The Group's most significant area of activity is its industrial gases business, incorporating a vast range of industrial, medical and special gases. Other major operating divisions specialise in distribution services, health care products and vacuum technology.
BOC is the world's second largest supplier of industrial gases and is the leading company in its field in the UK domestic market.
Innovation is an important cornerstone of BOC's operating philosophy. At one end of the scale, customers benefit directly from product and process innovations achieved by the company. Meanwhile both internally, and in conjunction with its suppliers, the company is constantly applying innovative processes to its business methods.
An example of the latter is the way in which BOC's European gases business, in conjunction with Visa and Company Barclaycard. has introduced a UK-wide charge card system to streamline its procedure for miscellaneous small purchases.
This document summarises the way this has been achieved to enable other interested organisations — including many of our own customers — to benefit from the experience gained by the company.
Trevor W. Rock
Materials Manager — BOC Gases Europe
Stefan J. Foryszewski
Purchasing Manager Regional Supplies — BOC Gases Europe
Current Purchasing Responsibilities
The structure of the purchasing organisation in BOC Gases Europe is as follows:
Central Purchasing
The Central Purchasing Team, located at the Divisional Head Office at Guildford, Surrey, has responsibility for negotiating and maintaining national purchasing agreements and issuing purchase orders covering the supply of high value or strategic goods and services to BOC Branches nationwide.
Regional Purchasing
Regional Purchasing Teams, located at each of four Regional Offices, have responsibility for negotiating and maintaining local or regional purchasing agreements and issuing local or regional purchase orders where the value is greater than £5.000. or for supplies not covered by Central Purchasing.
Order Placing
Order Placers are located at each of the Branches. The responsibility of the Order Placer is to generate and issue purchase orders and call off orders for supplies or services to that Branch up to the value of £5.000. Order placing is often combined with other non-purchasing duties.
Invoice Matching
Invoice Matchers are located at the Branches or Regional Offices. All invoices for the Branch/Region are forwarded to the Invoice Matcher. The responsibility of the Invoice Matcher is to process the invoice on the accounts payable system, matching for price and delivery. Following successful matching, invoices are released for payment, batched and forwarded to the Division's Financial Accounting Centre at Rotherham for validation and filing.
Cheques are released from the Financial Accounting Centre.
Systems
All purchasing and accounts payable activities are processed through an integrated mainframe system.
Low Value Purchase Orders
Overview of the Problem
As with many other organisations, considerable effort is expended by BOC in processing a large volume of requisitions, purchase orders and invoices that account for only a small proportion of the company's total expenditure.
Objective
To achieve significant improvements in the purchasing process for low value items in order to save time, reduce processing and paperwork costs, and generally streamline the overall purchasing operation
Facts and Dimensions
An analysis of historical data illustrates that 59.5% of BOC's transactions represented only 3.3% of expenditure.
The table below illustrates the relationship between the volume of invoices processed and the value of invoices processed by BOC, expressed as percentages of the total.
Cumulative % of Invoices processed by volume (% of total) |
Value band (£) of invoices processed |
Cumulative % of Invoices processed by value (% of total) |
23.4 |
0 — 50 |
0.3 |
37.8 |
51 — 100 |
1.0 |
59.5 |
101 — 250 |
3.3 |
74.7 |
251 — 500 |
6.6 |
96.2 |
501 — 5.000 |
26.7 |
99.0 |
5,001 — 25.000 |
44.5 |
99.6 |
25,001 — 50,000 |
57.2 |
99.8 |
50,001 — 100,000 |
65.2 |
100.0 |
100,001 & over |
100.0 |
BOC's Existing Purchasing Process
A requisition is raised prior to the acquisition of any goods or services. The requisition, raised by the proposer of the goods, must be authorised by the Cost Centre Manager or Authorising Manager. Requisitions consist of three-part sets.
A copy of the requisition is passed to the Order Placer.
The Order Placer inputs the requisition detail into the purchasing system, generating a four-part purchase order set.
A copy of the purchase order is issued to the supplier, against which the goods or services are supplied.
Upon receipt of the goods or services, confirmation of goods received is entered into the purchasing system by the Invoice Matcher or Stores Department.
On receipt of the invoice from the supplier, the invoice is entered into the Accounts Payable System and matched electronically against the relevant purchase order. If the invoice matches, then payment is made by cheque to the Supplier. If the matching process fails, then secondary authorisation is sought from the appropriate Cost Centre Manager or Authorising Manager.
This is the process hitherto employed by BOC for the processing of low value orders, and still employed where a charge card transaction is not practicable.
Options Considered
The following options were considered to cover the processing of low value purchase orders:
Local Purchase Order
Following receipt of an authorised requisition, a three-part local purchase order set would be handwritten or typed. The invoice would be matched manually against a copy of the order.
Copy Through Purchase Order From Requisition
Adding another copy to the requisition set (a fourth copy). This fourth part of the requisition set would become the purchase order which would be issued to the supplier. This would be handwritten. The invoice would be paid following authorisation by signature from the appropriate Cost Centre Manager or Authorising Manager.
Copy Requisition
A photocopy of the handwritten requisition would be issued to the supplier as the purchase order. The invoice would be treated as per the previously described option.
Daily Log Book
Purchase order details would be entered in a daily log book against predetermined purchase order numbers. No formal purchase order would be issued and invoices would be matched manually against the log book.
Verbal — Pay on Invoice Only
Goods would be ordered verbally with no formal purchase order. Invoices would be paid following authorisation by signature from the appropriate Cost Centre Manager or Authorising Manager.
Purchasing Card or Procurement Card
In addition to the above, the use of a charge card was considered.
With the exception of the charge card, each of the other options had been tried by BOC and had been deemed to be unsatisfactory due to the continued requirement to process large volumes of invoices and other documents.
Because it was felt that a charge card procedure would significantly diminish the need to process invoices, it was decided to pursue the charge card option.
Definition
In BOC terms, a low value purchase order which could be processed through the charge card procedure is defined as being:
■ Less than £250 (excluding VAT) per order.
■ Not covered by a BOC national or local purchasing agreement (except those released specifically for use via the charge card system).
■ Not a stock item. (Stock items require processing via the purchase order system in order to maintain electronic bin stock integrity.)
■ Not a personal expense item (eg hotel bill, petrol purchase etc.)
Examples of typical purchases qualifying for the charge card procedure would include branch consumables, vehicle spares, stationery, small tools, business-related newspapers and professional journals.
Appoint Purchasing Card / Procurement Card Holders
It is the responsibility of the Branch or Cost Centre Manager to appoint Charge Card Holders for that Branch. Card Holders include Order Placers and those members of staff who normally issue a high volume of purchase requisitions. People in this category include garage, maintenance, stores and building maintenance staff.
Supply of Purchasing Cards / Procurement Cards
Each appointed Charge Card Holder is issued with his or her own, individual charge card. The card carries the name of BOC and the Card Holder's name. Each card has its own maximum credit limit authorised by the appropriate manager.
Order Placing
The Card Holder places verbal orders on suppliers, and notes the requirement on a log (Appendix 1). It is incumbent upon the Card Holder to obtain, for each supply, a VAT invoice and associated Visa voucher which may be provided in advance or upon receipt of the goods. (In many instances these documents are combined.)
Credits
Where a credit is required from the supplier — for any reason — it is the responsibility of the Card Holder to obtain such credit and a credit note from the supplier. The credit will normally appear on the following month's statement.
Technical Item
Any item of plant equipment or service where failure would result in a significant impact on safety, product quality or plant performance is deemed to be a technical item. Where there is a need to purchase a technical item, the transaction must be processed by technically qualified staff. In processing the transaction a pro forma document must be completed and either telefaxed or posted to the supplier with all relevant associated documentation.
A copy of the pro forma document is forwarded to the Stores Department for Goods Inwards inspection.
The remainder of the process is the same as any other charge card transaction.
A copy of the proforma document is included as Appendix 2.
Purchasing Card / Procurement Card Statements
Each month the Bank issues individual charge card statements to each Branch Manager or Cost Centre Manager. The Manager passes each statement to the relevant Card Holder, who then attaches to the back of the statement all relevant invoices and Visa vouchers. The statement is then signed by the Card Holder and returned to the Manager.
The Manager reviews the statement, satisfies himself that all purchases were appropriate, and then authorises it. The signed statement is passed to the Invoice Matcher.
The statement provides the Manager with a summary of all of the Branch's low value expenditure for the month, together with supporting documentation (e.g supplier invoices).
In addition to the individual charge card statements, a composite statement summarising all individual statements is forwarded to the Financial Accounting Centre.
Tape Transfer of Information
When statements are issued, an electronic tape is also provided to BOC by Company Barclaycard. The tape carries all transaction details from the statements. The data from the tape is uploaded to the BOC mainframe data tables. Access to this data is then provided to BOC management via the company's standard query management facility. Data may be analysed/sorted by Card Holder, Supplier, BOC Branch, date or value. Exception reports are generated on a monthly basis.
The details contained on the tape form a major part of BOC's management information/control procedures for low value purchases.
Registration of Statements
Upon receipt of the authorised statement, the Invoice Matcher inputs the following statement detail to the Accounts Payable System:
■ VAT amount relative to the statement, calculated by summing the VAT amounts on the attached VAT invoices.
■ Appropriate cost code(s).
■ Total statement value.
■ Statement date.
■ Statement number.
The statement is then photocopied, the photocopy being retained by the Invoice Matcher for audit purposes. The original statement and all associated invoices and Visa vouchers are forwarded to the Financial Accounting Centre.
Reconciliation of Purchasing Card Statements
Upon arrival at the Financial Accounting Centre, individual statements are reconciled against the company summary statement.
Payment of Purchasing Card Accounts
Centralised payment is made to the Bank by Direct Debit seven days after the date of the statements.
Cost Coding
Each Branch or Cost Centre is provided with one or more charge card cost codes. When inputting the statement details into the Accounts Payable system, the statement is coded using these cost codes.
Should more detailed cost coding be required, then the Branch has the option/facility to cost code either each line of the statement, or to apportion the entire statement to a number of cost codes via predetermined percentages.
Purchasing Cards / Procurement Cards: Positive Issues
Fewer Requisitions
BOC targets the elimination of 30,000 purchase requisitions per annum.
Less Purchase Order Processing
BOC targets a reduction in purchase order processing of 30,000 per annum.
Less Invoice Matching
BOC targets the elimination of the need to match 50,000 invoices.
Supplier Data Maintenance
It will no longer be necessary to maintain and update supplier details on the Mainframe Purchasing System as settlement will be made via the Visa bank.
Less Cheque Processing
On average BOC issues one cheque for every four invoices. As payment for charge card transactions is made by the Visa Bank, BOC is generating fewer cheques.
Post and Stationery Savings
There are cost savings for the company in terms of postage, purchase order stationery, purchase requisition stationery and envelopes.
Staff Productivity Benefits
The amount of mundane administrative effort is being reduced and BOC staff have more time available to concentrate on core activities. Filing requirements in particular have been reduced.
Fewer Documents to Distribute
There is no longer the need to distribute requisitions, purchase order copies or copies of invoices for approval.
Improved Convenience and Speed
BOC staff are now more able to respond to the needs of the business and its customers.
Suppliers are Paid Sooner and No Disputed Supplier Invoices Either
Apart from the time savings, customer/supplier relationships are strengthened.
Purchasing Cards / Procurement Cards: Negative Issues
Cost Savings
The savings in time, processing and paperwork are estimated to exceed £200,000 per annum.
Retrospective Management Control
There is no internal authorisation process prior to expenditure.
Reduced Facility to Analyse Expenditure
Without looking at individual invoices. BOC managers not involved in the actual transaction are unable to establish the exact description of goods | ordered. Detailed spend analysis covering specifically described goods is therefore not possible at present.
Potential Abuse
The charge card can be used at any Visa Merchant. However, the controls applied (manager approval of statement process, financial audit etc.) to the procedure are sufficiently stringent to give a high degree of confidence that fraudulent use of the card would be exposed at an early stage.
Adverse Cashflow Effect
Payment is made via direct debit to Company Barciaycard sooner than normal BOC payment terms to suppliers. The payment cycle is therefore reduced, resulting in a cost of cash flow to the company.
Project Management
The project was managed and implemented by a Steering Group consisting of representatives from Purchasing, Finance, Information Technology and Quality Assurance Departments and a BOC Branch. Beneath the main Steering Group separate working parties considered other detailed aspects of the process for example:
■ Cost Coding
■ VAT Implications
■ BS 5750 Implications
■ Suppliers
Prior to full implementation and roll out of the process, commitment was sought and obtained from all levels of management within BOC Gases Europe and the parent company.
Timing and Milestones
August 1991 First formal steering group meeting
January 1992 Implementation at two trial sites
April 1992 Implementation at three further extended trial sites
July 1992 Implementation at one further extended trial site
December 1992 Agreement reached internally to roll out procedure
January 1993 Phased roll out commenced to all BOC Branches
August 1993 Roll out complete
Training
Training was undertaken at each Branch and was given to:
■ Card Holders
■ Requisitioned
■ Branch Managers and/or Supervisors
■ Invoice Matchers.
Charge cards were issued at the training sessions.
Each training session lasted approximately 3-4 hours.
Each Card Holder was presented with a booklet clearly detailing the process, its controls, the responsibilities of all parties, and what to do in the event of losing a card.
Feedback From Users
During the trial phases, formal feedback sessions were arranged with all trial Card Holders. Comments and criticisms were noted and actions taken on each point. Where possible, changes were made to the procedure to accommodate comments and experiences gained from the trials.
Suppliers
Considerable effort was invested by BOC Staff in discussing the procedure with suppliers and obtaining agreements to trade in this fashion.
Conclusion
Two years after the charge card purchasing project was first considered by BOC Gases Europe, and two months after the UK rollout has been completed, there is a population of 100 Visa cards throughout the division serving 30 branches plus head office requirements.
Initial indications are that the innovation has been a popular one among both BOC employees and the division's suppliers.
Following extensive national editorial coverage of BOC's experience there has been a high level of interest from companies of all sizes, including many who are already BOC customers.
Whilst we have endeavoured to respond promptly and thoroughly to every request for information, it is hoped that this document will provide the necessary guidance to other companies who are considering introducing a similar charge card procedure.
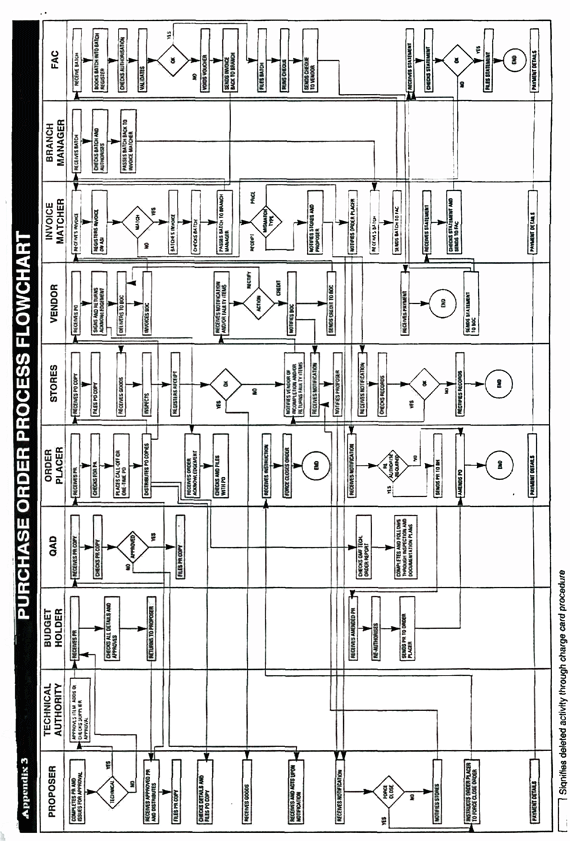 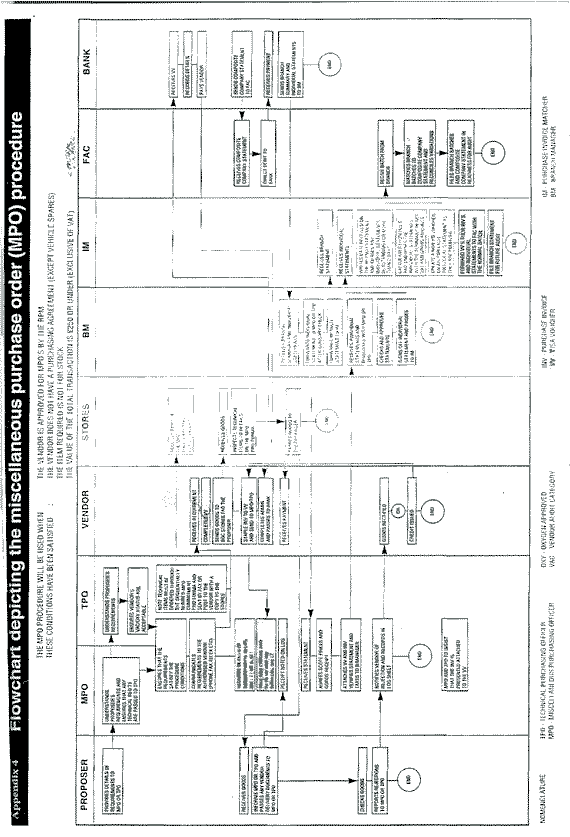
Contemporary Purchasing Card Implementation
By contrast, follow this link for a more contemporary approach to implementing procurement cards / purchasing cards.
© www .interim-management-purchasing.co.uk December 2012 |