Purchasing Intranet - Frequently Asked Questions - FAQs
Implementation / Valid From
These principles and procedures have been valid since the Oracle ERP system go-live on January XX 200X.
The Need for Change
Ordering
Types of purchase orders
Approval
Receipting
Invoices
Inquiries and reports
Non Standard Purchases
Payment Methods
Further Information
Q Why are these Changes Necessary?
Since non-stock / indirect purchases represent > € X0,000,0000 of the Client Company's cost of sales, it is essential that as the new Oracle ERP system is implemented that a more formal approach to the management of this spend is rolled out accordingly.
We're keen not to introduce unnecessary bureaucracy but to deliver the maximum benefit for the business. The Client Company must introduce a more structured approach to the non-stock / indirect" purchase to pay" procedures and tools; similar to those used by other similarly sized businesses.
“In the Client Company we spend as much on indirect goods and services as we do on raw materials and packaging, and at the moment across Europe our supplier base is surprisingly fragmented.
Even a 1% saving on our indirect spend will generate savings of hundreds of thousands of Euros per annum, year after year. So our investment in establishing an Indirect Purchasing Team and the necessary management tools and governance that Oracle ERP system will give us is no longer just 'nice to have'. It’s essential.”
Q. Why are we changing our Manual Purchase to Pay Processes ?
There are several disadvantages with manual Purchase to Pay Processes:
- Authorisation usually occurs only AFTER the purchase. For high value purchases this is too late.
- No legal protection because the Client Company's terms and conditions of business aren't used.
- Lots of administration, photocopying and paper, to send copies of 50% of invoices which are sent directly to Accounts Payable to Budget Holders and then back to Accounts Payable.
- Invoices can be mislaid or lost leading to delays in payment
- No recognised safeguards against possible financial impropriety.
Q. What are the major changes ?
A key change is that only Delegated Purchasers, or members of the Purchasing Team will be authorised to raise purchase orders.
Q What Are the Benefits of Introducing The new Processes?
- The Purchasing team will have more opportunities to provide added-value support for higher value purchases.
- The new Oracle ERP system process automatically embodies the "separation of three key roles" principle and therefore improves purchase-to-pay process governance.
- purchase orders will be sent to suppliers only if they are approved by budget holders before-hand, so...
- Signing invoices after the event will increasingly become unnecessary, so...
- Movement of paper invoices to and from the Client Company's accounting centres and budget holders will be minimised, so...
- The risk of payment delays to suppliers will be reduced as invoices are less likely to get held up or mislaid.
- Payment will only be made if the receipt of the goods or services is acknowledged / transacted by the Client Company.
- Having all purchase orders on the same system will enable the Finance team to better forecast enterprise-wide cash-flow.
- The addition of new suppliers will be controlled by purchasing to ensure that spend can be consolidated with Preferred Suppliers.
- The terms and conditions of contract on the back of the purchase orders will provide important legal protection to the Client Company, which in most cases wouldn't otherwise have been provided.
- Non-compliance with the new purchase-to-pay process will be formally monitored and managed.
Q. Where can I get a copy of the slides showing how to raise purchase orders ?
From here: Delegated Purchaser Oracle ERP system Training Slides. Tip: click on the appropriate link and then save the file to your desktop or another location before opening it. The slides are also shown on the "Tools for Purchasing" page.
Q. How do I Initiate the New "Non Stock" Purchasing Process?
Delegated Purchasers have been trained in the new Oracle ERP system about the purchasing procedures.
Anyone needing purchased goods or services may complete the "Purchase Requisition Template" (also on the Information and Standard Forms) page and then pass the completed form to their Delegated Purchaser. The Purchase Request Form is simply a means of communicating your requirements comprehensively to your Delegated Purchaser and therefore does not require any approval signatures.
The Delegated Purchaser will manage the purchase of goods or services up to their authorised limit. If the value of the purchase exceeds their authorised limit the Delegated Purchaser will pass the request to Purchasing.
Q. What will happen if the Purchase Request Form is not completed correctly ?
The Delegated Purchaser is likely to return the form to the originator for it to be completed which may delay the delivery of the goods/service.
Q. What is a discrete purchase order ?
"Discrete" purchase orders are those which are used for infrequent or non-repeating purchases - say less than four times per year. Although discrete purchase orders can be comprised of multiple lines and may have several receipt transactions associated with them, they are closed after the one-off goods have been delivered or the one-off services have been provided.
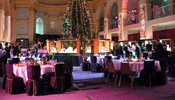
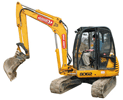
Examples include:
- Special Events
- One-off Hire of Plant and Equipment
- Fixed Price Consultancy Reports.
- Special Equipment
Q. What is an "open" purchase order ?
An "open" (sometimes known as a "blanket") purchase order is used when a type of purchase is repeated regularly (say more than four times per year). Rather than raising many discrete purchase orders or lines, and triggering the corresponding number of approval transactions, an open purchase order is raised once, and is approved once. For this reason, open purchase orders last not just for a single event as "discrete" purchase order lines do, but for extended periods of time: typically a year. In doing so, open orders eliminate the maximum number of transactions to raise discrete purchase order lines and have them approved. Only the number of receipting transactions remain the same as an equivalent number of discrete purchase orders.
Because open purchase orders are for reoccurring purchasing events, they are often raised for higher values and therefore will often raised by the Purchasing team.
Q. What is a "bottom up" purchase order construction?
Where unit prices are simple (e.g. price per day, price per hour), the value of the open order can be constructed "bottom up" from the estimated usage x unit price, presuming that receipting can be transacted in the same way (by units). Examples of where this may be possible include:
- Milk (price per bottle)
- Buffet Lunches (price per person)
- Cleaning Services (price per service event or price per person hour)
- Garden Maintenance Services (price per service event or price per person hour)
- Planned / Preventive Engineering Maintenance Services (price per event or price per person hour)
- Consultancy or Interim Management Services (price per day)
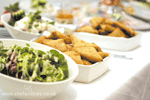
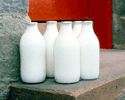
Q. What is a "top level estimate" purchase order construction?
In some cases even if the unit prices for the individual "components" are known, the mix of usage can be difficult to predict e.g.:
- The mix of partners, solicitors and associates for a legal consultancy project
- The mix of partners, senior auditors, and auditors for financial auditing
- Etc.
In other instances pricing mechanisms can be a complex mix of fixed and unit prices e.g. mobile phones:
- Monthly line rental
- Domestic call rate (peak and off-peak)
- International call rates (peak and off-peak)
- Data call rates
- Text rates
- Handset upgrades
In such cases trying to build a "bottom-up" estimate of usage is difficult, to say the least. Instead we'd recommend raising open (or blanket) orders based upon a "top level estimate" of the spend. This will normally take the form of the total spend in for the period covered by the open order. However, it is necessary to remember that receipting is transacted not by value, but by volume. As such, if an open purchase order for a cost-centre is raised (say) for Taxis to cover a period of a year up to a value of € 2,750 and the purchase order is constructed as:
Line 1: Description: Taxis for One Year. Unit of Measure: Each. Quantity:1. Unit Price: € 2,750. Total Value: € 2,750.
Then only one receipt (whether for a trip, a month's trips or the whole year's trips) can be transacted against this purchase order/line with the quantity: 1. To receipt multiple taxi trips against a single purchase order line, it would be necessary to construct the open purchase order in the following way:
Line 1: Description: Taxis for One Year. Unit of Measure: Each. Quantity: 2750. Unit Price: € 1. Total Value: € 2,750.
Then, if necessary, the value of each Taxi trip can be receipted individually, by receipting a proportion of the 2750 "Quantity" which approximates the value actually used. The receipted volume should be rounded up to cover the receipted value, so if the value of the trip was € 45.14, then 46 units should be receipted.
Q. What's the difference between "bottom up" & "top level estimate" purchase orders ?
There are several advantages to constructing purchase orders in a "bottom-up" manner. Firstly, the more detail shown on a purchase order, the easier it is for the Purchasing team to compare pricing for similar purchases across Europe. Secondly the receipting transaction can be done by the Delegated Purchaser without reliance on a prompt from the Accounts Payable team, since the Delegated Purchaser knows how many bottles of milk, buffet lunches, days of consultancy services etc. have been provided. As such, as soon as the invoice referencing the purchase order number, is received by Accounts Payable, the invoice can be paid.
By comparison unlike the receipting transaction for "bottom-up" purchase orders, the receipting transaction for "top level estimate" purchase orders, cannot occur independently. Since it is only when the invoice has been received by Accounts Payable and they have seen that the corresponding receipting transaction hasn't yet occurred that they will provide the Delegated Purchaser with a copy of the invoice so that the receipt can be transacted. When the Delegated Purchaser receives the copy of the invoice they can receipt the quantity to approximate the value of the copy of the invoice provided by Accounts Payable. When the receipt has been transacted, the Delegated Purchaser must inform Accounts Payable so that they can pay the invoice. If Accounts Payable aren't told that the receipt has been transacted it may result in a payment delay.
There are several disadvantages then to the use of the "top level estimate" method of PO construction. Firstly it involves considerable additional work for Accounts Payable. They have to scan or copy the invoice and send it to the Delegated Purchaser to prompt the receipting transaction. Additionally the Delegated Purchaser must then inform Accounts Payable once the receipting transaction has been completed. Furthermore, it is impossible for the Purchasing team to make comparisons between prices paid across Europe for goods and services using purchase orders constructed using the "top level estimate" method.
Q. Why should I not always send a supplier my "open" purchase orders?
It can be risky to send suppliers "open" purchase orders, because it can declare to them what the Client Company's approved budget is for the particular purchase.
For example, if a "top level estimate" "open" purchase order is raised and approved for a value of € 10k and is then sent to the supplier, then it is possible that the supplier may increase their pricing to use as much of the approved € 10k value as possible. It is for this reason that "open" purchase orders constructed using the "top level estimate" approach should NOT be sent to suppliers. Instead, an example is shown below of how an email can be constructed to communicate some of the key non financial information to the supplier - in this case, on behalf of the Client Company Limited.
Please find the Client Company's purchase order number below for: [description of goods or services]
Purchase Order Number:
XXXXXXX ON 04401
To ensure prompt payment please ensure that:
1. all invoices reference this purchase order number and:
2. all invoices are sent to:
Accounts Payable Department
the Client Company
Address
United Kingdom
Please find the enclosed link to the Client Company's standard terms and conditions of business which shall apply to this purchase order: http://www.the Client Company.com/data/about the Client Company/the Client Company-Limited-TCs.pdf
Notice that because the "open" purchase order isn't being sent to the supplier and that therefore the supplier would not otherwise receive a copy of the Client Company's terms and conditions (which are printed with it). The above email ensures that the supplier is nevertheless informed that they apply.
"Open" purchase orders which are constructed using the "bottom-up" method can be sent to the supplier but only if the header of the purchase order clearly states:
"This Purchase Order does not represent a commitment by the Client Company to purchase the entire quantities stated herein. Any quantities shown are the maximum potential quantities which may be ordered by the Client Company".
Q. The supplier that I want to use isn't on the Oracle ERP system. What do I do?
the Client Company's spend has historically been substantially fragmented between many suppliers which often provide similar goods/services, not least because different parts of the business simply weren't aware that others were using alternative suppliers for the same things.
A fragmented supplier base is substantially more difficult and more costly to manage effectively. Improvements in quality, cost and delivery are more difficult to achieve if spend isn't consolidated. Supplier duplication also creates additional unnecessary workload for the Accounts Payable team. As such, it is often beneficial to consolidate suppliers (where appropriate) and prevent unnecessary fragmentation in the future.
To prevent unnecessary fragmentation of the supplier base it is necessary to manage consolidation and any supplier additions with a business-wide understanding of the capabilities of the existing supplier base. Over time, working with internal customers and using a mix of tactical and strategic purchasing processes, the Purchasing Team will consolidate fragmented spend with Preferred Suppliers. Delegated Purchasers should whenever possible purchase from preferred suppliers for categories of expenditure for which they have been selected.
Of course any employee may recommend the addition of a new supplier on behalf of the business using the appropriate "Supplier Proposal Form" (also on the Information and Standard Forms page). However, to prevent unnecessary supplier fragmentation additions to the ERP Programme supplier address book must only be made with the authorisation of the Purchasing Team.
This restriction DOES NOT APPLY to purchasing card purchases. New sources can be added by Delegated Purchasers because the value of purchasing card spend overall is <2% of the Client Company's purchased expenditure and only one credit card statement is transacted, rather than numerous supplier invoices.
Q. Can Delegated Purchasers raise more than one purchase order for < € 3,000 for the same purchase?
No. Raising two purchase orders each for say € 2,500 for the same purchase would be viewed as a non-compliance with the Client Company's procedures.
Q - Can I raise one purchase order against more than one cost centre?
Yes. The costs of purchases can be shared with other cost centres by identifying them in the individual lines of the purchase order. However, this can be done only if the cost centres are within the same Oracle ERP system company code. For different cost centres in different company codes the current financial cross charging process will still apply (refer to Finance for guidance).
However, irrespective of the cost centres listed in the lines of the purchase order, the cost centre input into the header is the one associated with the PO's approval route. If the approval routes for the cost centres referenced in the lines of the purchase order have different approval routes from the purchase order header's cost centre, then approval must be obtained independently from the Approvers of the other cost centres. Their acceptance (or otherwise) will then need to be communicated in writing to the Purchasing team member or Delegated Purchaser before the order can be raised.
Q. what's the difference between "of" and "on" purchase orders ?
In addition to the more usual ON type (non stock) purchase orders, OF type orders are used to purchase Fixed Assets. These OF type purchase orders are similar to the ON type orders except that they include the Fixed Asset number.
There are special approval routes for M&S OF purchase orders.
An OF order type is used if the purchase is:
- a single piece of equipment above the capital threshold value (£ 500 in the UK) and for which a capital approval exists.
- part of a wider project and is listed as part of the approved CIP for that project. In such cases the capital threshold value does not apply.
An ON order type is used if the purchase is:
- a single piece of equipment below the capital threshold value.
- for the ongoing maintenance and/or repair work of capital equipment.
Note - In certain circumstance the refurbishment of a piece of equipment can be a capital project in it’s own right.
Q. Where can I get a copy of the guide about approving purchase orders ?
From here: Guide to Approving purchase orders in Oracle ERP system. Tip: click on the appropriate link and then save the file to your desktop or another location before opening it. The document is also shown on the "Tools for Purchasing" page.
Q. Where can I get a copy of the guide about delegating approval authority ?
From here: Guide to Delegating Approval Authority. Tip: click on the appropriate link and then save the file to your desktop or another location before opening it. The document is also shown on the "Tools for Purchasing" page.
Q. where's my PO during the Approval process - who has / hasn't approved it ?
To see who the purchase order is waiting approval from: use the "Approve Non Stock POs" screen, put an asterix (*) in the "Approver" field, check the "Waiting Approval" box and type in the purchase order number and click "Find".
To see the entire approval structure for an order - follow the above steps, then after clicking the "Find" button, select the line and click on the "Status Summary" button on the exit bar.
Q. How will orders get approved ?
Where purchase orders are used, the approval of these purchases will now take place within the new system, before the purchase is made, rather than after the event. See the guide: "Approving purchase orders in Oracle ERP system" (also on the Tools for Purchasing page).
When a purchase order has been raised by a Delegated Purchaser or by the Purchasing team, the appropriate approver will automatically receive an email in Outlook informing them that the purchase order needs to be approved. Cost centre approval routes are managed by Finance. Queries about the purchase order approval process should be made to the appropriate Finance Manager.
Approvers should log into the new system and review the orders waiting for their approval. The approvers will Approve or Reject these orders as they deem appropriate.
Q. why can't I approve my own purchase orders ?
If you're a Delegated Purchaser AND have delegated authority to authorise expenditure for a cost centre, Oracle ERP system won't allow you to authorise your own purchase order because of the "Separation of the Three Key Roles" governance principle. In such cases the authorisation email will be sent to the next highest cost centre approver in the authorisation chain nominated by Finance. Cost centre approval routes are managed by Finance. Queries about the purchase order approval process should be made to the appropriate Finance Manager.
Q. What happens to a purchase order once it’s been approved ?
Once a purchase order has been approved at all the required levels (or rejected at any level) an email will be sent automatically by the system to the person who created the order informing them of this event. If it has been approved it will be sent to the supplier, in most cases by autofax or email.
Q. What if I want to change a purchase order after it has been approved ?
Once a line on a purchase order has been approved no further changes can be made to that line other than the line being cancelled. However, a Delegated Purchaser can add lines to an existing approved purchase order but these added lines will have to go through the same approval process, just like the previous lines did.
Q. What if I need to order something and I know the approver is out of the office ?
When an Approver plans to be out of the office they can delegate their approval authority to someone else by following the guide: "Temporarily Delegating Approval Authority in Oracle ERP system" (also on the Tools for Purchasing page).
The person to whom temporary authority to approve purchase orders has been delegated must return the authority as soon as the original approver is back. The rules regarding who this authority can temporarily be delegated to are governed by the Finance team. Queries regarding purchase order approval routes should be made to the appropriate Finance Manager.
Approval of Oracle ERP system purchase orders can not be carried out via Blackberries but can be carried out if the Approver is able to remotely access the network (for example from home) or where the Approver is located in the Client Company offices in the UK, France, Germany, Belgium or Holland.
As the new system and processes are implemented it is inevitable that there may be need to make adjustments to the processes to enable a better fit to the needs of the business. Any changes that are made will be communicated as appropriate.
Q. What happens when the goods or service is delivered ?
Upon receipt of the goods the originator of the Purchase Request must sign any accompanying delivery notes and pass the Client Company’s copy of these to the Delegated Purchaser as soon as the goods have been received. The Delegated Purchaser needs this proof of delivery to ensure that the supplier is paid.
Q What should I do if there is no delivery note ?
Where a delivery note has not been sent with the goods, or where the purchase involves a service, the originator of the purchase request must send an email to the Delegated Purchaser informing them that the goods or service have been received, indicating the quantity received and confirming the goods have been accepted or that the service has been delivered.
Q - What if the supplier refuses to quote our purchase order number on their invoice?
In this case the purchase order should be raised in line with the relevant purchasing process. Once the invoiced is received without the purchase order number, if Accounts Payable can't identify the purchase order number without assistance, a scanned copy of the invoice will be sent through to the department who have initiated the purchase. At this stage the Delegated Purchaser should receipt the goods or service in the usual manner but should advise Finance of the purchase order number when confirming that the receipt transaction has been completed.
Should the above situation occur it is recommended that you contact your local Purchasing team member for them to discuss the matter further with the supplier as failure to quote a purchase order number could result in delayed payment for the supplier.
Q - What do we do if the supplier refuses to issue an invoice?
If a supplier will not provide an invoice to allow Finance to match against a purchase order then the requisitioner will need to agree the approach with their local Accounts Payable team. For example, an alternative form of payment may be requested, but permission to use this approach in this instance should be obtained from the Accounts Payable team.
Q. How can I run a simple inquiry / report about my purchase orders ?
purchase order lines can be exported to Excel in a straight-forward manner. Simply go to the relevant purchase order Inquiry icon within the Oracle ERP system menu structure: e.g. "Non Stock (ON)" or "Fixed Asset (OF)", then, in the first screen, input the appropriate cost centre into the "Branch/Plant" field and select "Find". This lists all of the purchase order lines which have been raised on behalf of that particular cost centre.
Select the top purchase order line that you wish to export to Excel by clicking on its left edge and then pressing the "Shift" key whilst scrolling down to the bottom PO line that you want to include by again clicking on its left edge. The range of lines that you wish to export to Excel should now be highlighted. With the range of purchase order lines highlighted, right click the mouse to select the option/s to export the lines to Excel and then confirm this when requested.
The selected purchase order lines will then be exported to Excel. Note that the Excel application to which the rows are exported is not your usual Excel application. You may wish to then cut the exported rows and paste them into your own Excel application before manipulating the data.
Q. Are there any exceptions?
Yes. For example, fuel cards and expenses/credit cards are used by employees who usually aren't either Delegated Purchasers or members of the Purchasing team. Nevertheless, they are subject to complementary rules for internal control.
From time to time though, most usually as a consequence of the introduction of a new supplier, further exceptions may be introduced. In each case these exceptions are formally agreed between Finance and Purchasing. For example, following the introduction of Expedia as the Client Company's global travel agency, it has been agreed that the Expedia on-line booking tool replaces the need to raise Oracle ERP system purchase orders for such travel transactions.
Similarly, for the ongoing monthly fixed price element of contract hire leases for fleet cars, Purchasing and Finance have agreed another bespoke solution.
Q. I used to request cheques to pay suppliers. Can I still do this?
Please be aware that non PO based payment requests must only be used in exceptional circumstances. This is not the Client Company's preferred approach. Nevertheless, if for example, an entirely unique payment needs to be made to a new supplier which can't accept a Purchasing Card payment, it wouldn't be worthwhile completing a "Supplier Proposal Form" (also on the Information and Standard Forms page) and then setting a new supplier up on Oracle ERP system for just one payment transaction. Under these circumstances a "Payment Request Form" may be submitted (also on the Information and Standard Forms page). Tip: click on the appropriate link and then save the file to your desktop or another location before opening it.
Q. How do we handle the purchase of goods and services by Direct Debit?
A direct debit is a means of payment rather than a purchasing process and would be set up by Finance after the initial purchase has been approved. (If payment by direct debit is optional then it should only be agreed to if there is an incentive to do so, e.g. prompt payment discount. Please consult with Finance for further guidance in such circumstances)
Therefore the relevant purchasing process should apply regardless of the fact that we are paying by direct debit and this would depend upon the type of item being purchased. There are two main areas where direct debit payments are expected to apply - leases, and services such as utilities.
For services such as utilities e.g. electricity, these items should be covered by a blanket order probably utilising an top level estimate methodology based upon the budgeted figures. Although payment is made by direct debit Accounts Payable should still receive an invoice to cover the item being purchased. This should be matched against a purchase order and a receipt should still be made to confirm the item has been provided to the end users satisfaction.
In the area of leases it has been agreed that for the recurring fixed cost element the purchase would not require a purchase order to be raised. The contract would however need to be validated by the Purchasing team to confirm it has been reviewed and authorised in line with the Approval Routes before being signed by an officer of the company.
Q - How do we proceed when the supplier requires pre-payment for the goods or services?
To purchase goods and services by making a prepayment the relevant purchasing process for the type of item being sourced should be followed and the purchase order number forwarded to the supplier in the usual manner. The supplier should be asked to send an invoice (referencing the purchase order number) to Accounts Payable. Upon receipt of the scanned copy of the invoice from Accounts Payable (but before the receipting transaction) the Delegated Purchaser should obtain from the budget holder an email authorising a receipting transaction in the Oracle ERP system (Oracle ERP system) system before the actual receipt of the physical goods or services. Once this confirmation is received the Delegated Purchaser should receipt the item in Oracle ERP system. Once completed they should confirm to Finance that the receipt has been completed in the system and should include a reminder that it represents a prepayment.
NB. To enable Finance to account for the prepayment it is vital that the fact that a prepayment is to be made must be clearly stated on the purchase order and the supplier's invoice.
Alternatively if the purchase from this supplier will be unique (and say not repeated next year) then a an alternative form of payment may be requested.
Q Who is my "Delegated Purchaser"?
Each cost centre should have at least one Delegated Purchaser assigned to it. Please see the list of Delegated Purchasers.
Q. I've got another question about the purchasing process. Who can help me ?
For questions relating to branch-plants / cost centres, PO approval route structures, account codes etc. please get in touch with your local Finance contact (below) who will refer your question to the appropriate person:
- Global HQ (Clinical Development, PM&TD, Medical and Regulatory) - Pxxxx Sxxxxxxxx
- Global HQ (Finance, IT, Facilities, Corporate and HR) - Nxxxx Bxxxx
- Global HQ (CCO, Global Marketing, Commercial Planning and Business Development) - Rxxxxxx Mxxxxxxx
- Global HQ (MSE UK) - Rxxxxxxxx Hxxxxx or Pxxxxxx Rxxxxx
- Global HQ (NPL / UK BU) - Sxxxxxxx Dxxxx
- UK Plant (M&S) - Gxxxxx Pxxxxxxx
- UK Plant (non-M&S) - Pxxxx Rxxxxxx
- French Plant (M&S) - Jxxxxxx Lxxxx
- French Plant (non-M&S) - Mxxxx Lxxx Gxxxxxxx
- Paris (France Commercial) - Sxxxxxxx Txxxx
- Paris (M&S) - Nxxxxxxx Dxxxxxx-Mxxxxx
- Amsterdam (M&S) - Exxxxx Mxxxxxx Lxxxxxxx
- Amsterdam (BV Corporate) - Sxx Bxxxxx
- Amsterdam (Commercial) - Rxxxxxx Hxxxx
- Brussels (Commercial ) - Rxxxxx Hxxxxxxxx
- Brussels (non-Commercial) - Axxxxx dx Cxxxxxxx
- German Office (Germany, Austria, Switzerland ) - Pxxx Lxxxxx
Questions relating to raising, printing and receipting of POs and approval training should be directed to the following members of the Purchasing team:
- Global HQ - Sxxxxxx Cxxxxxxx
- UK Plant - Sxxxxxx Cxxxxxxx
- French Plant - Vxxxxx Cxxxxxxxxx
- Paris - Vxxxxxxxxx Cxxxxxxxxx
- Brussels - Pxxxxxxxx Vxxxxxxx Exxxxxx
- Amsterdam - PxxxxxVxx Exxxxxx
- German Office - Dxxxxx Rxxxxxx
Q. What is the difference between "stock" and "Non-Stock" Purchases ?
The Oracle ERP system differentiates between purchases for "stock" purchases (the stock levels of which are formally managed by the Oracle ERP system) and "non-stock" purchases (whose stock levels aren't formally managed within the system). For example, the stock levels of the materials that are bought for production are formally managed in the Oracle ERP system. These are therefore "stock" purchases.
As such, most of the goods and services purchased for the Client Company offices are "non-stock" purchases, even things like stationery for example, which although they are stocked, aren't managed using Oracle ERP system's formal stock management functionality.
the Client Company's "non-stock" purchasing process is different from its "stock" purchasing process, in that "non-stock" purchases must be authorised by budget holders before being purchased. "Stock" purchases don't need to be authorised in this way because the business is simply purchasing to replenish pre-authorised inventory levels.
Q. What is the Difference Between "Direct" and "Indirect" Purchases?
"Direct" purchases are those which are used as components in the manufacture the Client Company's products including raw materials and product specific packaging components (e.g. display cartons etc.).
Quite simply "indirect" purchases are those which aren't "direct" purchases. This includes services, (e.g. catering, travel, security, cleaning etc.) but also goods that are not used as components in the manufacture the Client Company's products (e.g. engineering spares, office equipment, stationery, personal protective equipment (PPE), generic packaging components e.g. pallets and shrink-wrap etc.).
Q. What is the Difference Between "Direct" and "Indirect" Purchases and "Stock" and "Non-Stock" purchases?
Not a great deal really. Most "direct" purchases are "stock" purchases and most "indirect" purchases are "non-stock" purchases. However to be precise, some "indirect" purchases such as personal protective equipment (PPE) and engineering spares are "indirect" purchases but are managed using Oracle ERP system's formal stock management functionality and so are "stock" rather than "non-stock" purchases.
Q. Will it cost the Client Company more to send purchase orders?
By sharing the workload amongst numerous Delegated Purchasers and introducing Purchasing Cards we don't expect to need to invest in additional headcount. However, if the Client Company didn't use the Delegated Purchasers approach, then a much bigger Purchasing organisation would be needed, which would inevitably slow many purchases down and only save marginally more than the proposed approach.
Some have specifically asked about postage costs. Will we spend more on postage? The Oracle ERP system is capable of faxing and emailing suppliers if their details are entered into Oracle ERP system. If a supplier's email address is used, then purchase orders can be sent for almost no additional cost. Alternatively even sending purchase orders by autofax will save Delegated Purchasers the time that would otherwise have been taken printing and posting the purchase orders.
Q. Where can I find copies of the Client Company's Standard Terms and Conditions of Contract ?
the Client Company has a variety of standard terms and conditions of contract.
The terms and conditions used for the Client Company's purchase orders are published on the main the Client Company website.
However, the Legal Services team are also developing an increasing library of model contracts for different supplier relationships. These include 1. Manufacturing and Supply Agreements and 2. Quality (or Technical) Agreements for the following categories of direct materials:
- Active Pharmaceutical Ingredients (APIs)
- Excipients
- Packaging
Further contract models have been developed for indirect goods and services. These model terms and conditions will be made available on the Client's Intranet site and updated from time to time by the Legal Services team as appropriate. Any terms and conditions of contract made available in this way must not be modified and sent to suppliers without the approval of the Legal Services team, except that members of the Purchasing team (not including Delegated Purchasers) may modify square bracketed commercial variables, for example in Commercial Schedules of the Agreements.
Q. How do I print the files shown on these purchasing the Client's Intranet site pages ?
When you first click on a particular form you are presented with the option shown below:
At this point rather than click "Open" (which will open the file within the the Client's Intranet site frames) select "Save". This will give you the option of saving the selected file to one of your drives or folders.
Once you have saved the file to a convenient location go to the relevant package e.g. Word and open the newly saved file from there. You can then print the file using the standard File, Print functionality. Additionally you can complete the form electronically rather than hand write it and have the option to save say completed requisitions electronically. However, when using a form in this way please remember to periodically check the Client's Intranet site to ensure you continue to use the very latest version of the forms.